In today’s fast-paced manufacturing environment, maintaining consistent product quality and high-speed output is a constant challenge. Many manufacturers overlook glue application, even though it plays a critical role in packaging performance. That’s where HHS glue Systems come in — a game-changing solution that ensures accurate glue placement and eliminates adhesive-related errors.
5 Reasons to Switch to HHS Glue Systems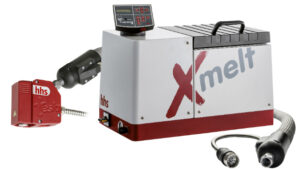
1.Speed Without Compromise in Packaging Lines:
- No dripping, skipping, or adhesive waste
- Consistent results even in 24/7 operations
2.Precision That Powers Modern Packaging:
In today’s fast-paced manufacturing world, precision and consistency are critical — especially when it comes to adhesive application. HHS hot melt gluing systems, including hot melt glue dispensers and cold glue solutions, are engineered to meet the demanding standards of high-speed packaging lines because even minor glue errors can lead to major production issues.
They’re trusted across industries like folding cartons, envelopes, pharma labeling, and print finishing — not just for speed, but for flawless bonding every single time. And while many systems promise reliability, HHS actually delivers it.
Consistent Application. Zero Rework.
Thanks to advanced DotJet technology, HHS glue systems apply adhesive in clean, accurate lines or microdots, ensuring consistent results — even at full speed.So, you can maintain output without sacrificing quality, and you won’t need to worry about production losses because of glue misapplication.
-
No dripping or overspray
-
No misalignment or glue overflow
-
No rework or production delays
3. Benefits of Glue Monitoring in Packaging Lines:
- Zero Defect Packaging: Glue sensors detect defects in real time, allowing for immediate correction — because even a small adhesive error can compromise product quality.
- Reduced Rework and Scrap: It saves time and materials, but more importantly, it improves overall production efficiency, so your packaging line runs smoother and more cost-effectively.
- Lower Operating Costs: By minimizing downtime and glue usage, companies not only save on costs but also improve operational efficiency — because less disruption means more consistent output, and so they achieve a faster ROI.
- Compliance & Consistency: Glue monitoring is especially vital for pharma and FMCG, where every seal must meet strict safety standards — because even a minor adhesive error can lead to compliance issues and product recalls.These industries demand precision and consistency, but without the right monitoring system, maintaining both can be challenging, so HHS glue systems offer the accuracy and control needed to ensure quality and compliance.
4. Seamless Integration with Existing Systems:
Manufacturers can add HHS glue systems to existing industrial glue systems, folder gluers, or labelers — because their modular design simplifies integration into various production setups.
The interface is user-friendly and intuitive, so operators can adapt quickly without lengthy training.
They reduce installation time and learning curves, but still deliver advanced monitoring capabilities and precision — and that means minimal downtime with maximum efficiency.
5.ROI Through Reduced Downtime:
Maximizing uptime is critical in fast-paced packaging and labeling environments, because even short interruptions can impact productivity and profitability.HHS hot melt gluing systems, distributed and supported by Omkar Systems, are engineered for reliability, efficiency, and long-term cost savings.
They feature durable components and intelligent glue control — so manufacturers can reduce waste, avoid unplanned stoppages, and extend equipment life.
These benefits don’t come at the cost of performance, but rather enhance it — and that’s why they contribute to a faster, more measurable (ROI)return on investment.
Key ROI Benefits:
-
Smart glue controllers optimize adhesive usage per unit.
They reduce glue waste and improve application consistency — and they’re easy to configure with intuitive controls.
So, manufacturers get efficiency without sacrificing control. -
Fewer breakdowns and longer-lasting parts mean less maintenance — and more uptime.
They’re built for durability, so performance stays consistent even under pressure. -
Consistent glue application eliminates costly rework — because each product is bonded right the first time.
It saves time and material, and it keeps production flowing. - Improved production efficiency in high-speed lines means more output and fewer delays.
The system runs fast and accurately, so there’s less downtime.
Because everything stays on track, your team meets targets — but without sacrificing quality.
Conclusion:
Whether you’re running a high-speed packaging line or managing delicate labeling tasks, a glue monitoring system is essential for long-term quality and efficiency. HHS glue systems deliver speed and accuracy, but without the complexity.
So, when combined with the integration expertise of Omkar Systems, you get a solution that performs reliably because it’s built for real-world packaging demands.
Want to see glue monitoring in action? Schedule a free demo or technical consultation with Omkar Systems today.